If you’re new to 3D Printing or have never upgraded your machine’s hotend it can be intimidating will all the conflicting information out there. In this article, I’ll break down the most common type of HotEnds, extruders, and how they work together in your 3D Printer.
The Proprietary Hotend
This is the type of hotend I try to avoid at all costs! I’m pro open source so when I see a manufacturer create a sub-par hotend that is 5x the cost of other ones it just sucks! It’s these companies that stunt the growth of industry innovation.
Anyway… These types of hotends are custom designed to the 3D Printer and will need to be OEM replaced if damaged or you will need to find a way to adapt another hotend type.
Here are some examples of proprietary hotends:
Now I’m not saying these proprietary hot ends don’t work. Well most work, kind of… These are great options for consumers that want a printer that works “out of the box” as if such a thing exists for 3d printers.
Just do your research before buying about these hotend known issues. Know that when the part needs to be replaced that it will cost you. A little googling and the willingness to learn will pay off big time in the long run.
The Open Source “RepRap” HotEnd
These types of hotends are both low-cost and designed to be compatible with most 3D Printers.
In terms of adaptability, the most popular type is the J-Head MK style. This is the design of the shape that mounts to the 3d printer’s carriage mount.
The image to the left is a typical example of the J-Head mounting profile. There are many adapter and 3d Models for mounting solutions. Check out Thingiverse for free stl files to print for your machine.
These are styles that E3D-online and most clones are made with. There is a ton of information and tutorials on how to use these hotends. Check out the RepRap HotEnd Comparison wiki to see the variety of types.
Geared Extruders
Earlier 3D Printers used Geared Extruders which are still frequently used today. Greg Wade’s Geared Extruder pioneered this design and the parts are even 3D Printed!

A more modern innovation from E3D is the Titan Geared Universal Extruder with newly added Aero Heatsink.
The advantage to the Geared Extruders is it puts less strain on the NEMA stepper motor and also makes it run much cooler. Geared Extruders also are able to exert more extruding torque which is great for filaments that require some extra push.
Direct Drive Extruders
A direct drive extruder is where the filament is driven by a “hobbed” gear that is directly attached to the NEMA Stepper Motor. Today’s 3D Printer stepper boards and controllers make the NEMA 17 motors perfectly capable of exerting enough force for the filament to be pushed properly and not overheat the motor.
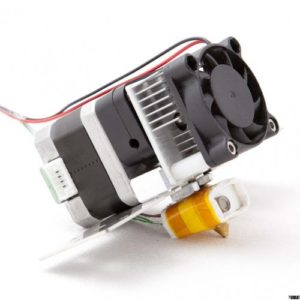
If you’d like, you can also print a customized direct drive extruder for an E3D hotend (typically used on Prusa 3D printers). Be sure to print your models in ABS or other high temp filaments as PLA will melt!
Bowden Extruders
A bowden extruder is where the motor is positioned away from the hotend. This is done with a PTFE Tube that guides the filament into the hotend.
The Tube is sized so the motor still exerts force to properly push the filament into the hotend. The advantage to Bowden setups is the carriage has less weight on it as the motor is usually mounted to the 3d printer frame. This helps the linear motion and can improve print speed and quality if tuned correctly.
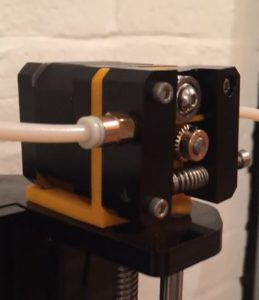
Bowden extruders are most commonly used in Delta Style 3D Printers and Cartesian printers, such as the Creality Ender 3 3D Printers. But these days I am seeing both types used for all makes and models. It all comes down to user preference.
One challenge is properly setting up your STL slicer software to properly extrude the filament without leaving any blobs or artifices. This is primarily done by adjusting the retraction speed and retraction distance settings in your slicer.
Summary
So it really doesn’t matter which category or type of extruder you choose. What’s most important is that you understand how it work and how to properly tune the setting of your machine to make things work. I’ll leave you with this video from one of my favorite 3D printer guru’s Thomas Sanladerer.